Achieve Superior Quality with Pre-treatment Drum & Heating
Product Description
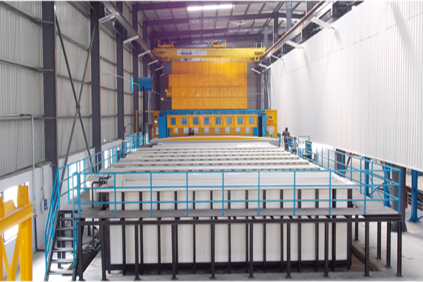
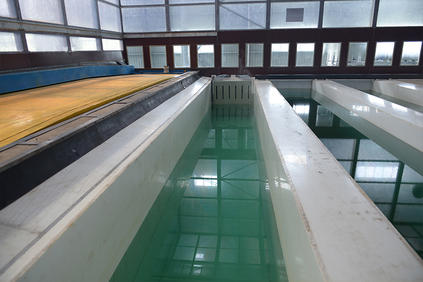
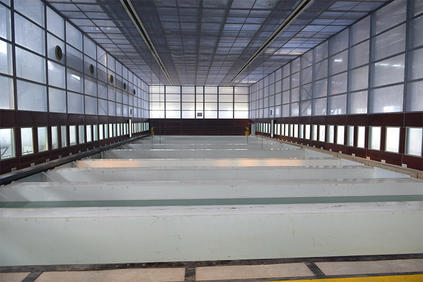
- Introducing our revolutionary pre-treatment drum and heating system. As pioneers in the hot-dip galvanizing industry, we understand the critical role that pre-treatment plays in ensuring the highest quality of galvanized products. With advanced technology and innovative design, we aim to revolutionize the way pretreatment is done.
Traditionally, the domestic hot-dip galvanizing industry has relied on concrete and granite pickling tanks for pretreatment heating. However, with the introduction of cutting-edge hot-dip galvanizing technology in Europe and the United States, demand for more efficient and reliable alternatives continues to grow. This is where our PP (polypropylene)/PE (polyethylene) pickling tanks come into play.
Our pretreatment drums and heating systems combine the basic processes of degreasing, rust removal, water washing, plating additive application and drying into one seamless operation. With this all-in-one solution we eliminate the need for multiple storage tanks and simplify the entire pretreatment process. This not only improves efficiency but also reduces operating costs.
The main advantage of our pretreatment drums and heating systems is the use of PP/PE materials. These materials are known for their excellent resistance to corrosion and chemical degradation. As a result, our pickling tanks offer superior performance and durability compared to traditional concrete tanks. The use of these materials also ensures that our systems are environmentally friendly and comply with international environmental standards.
In addition to using high-quality materials, our pretreatment drums and heating systems are equipped with state-of-the-art heating technology. This ensures precise and consistent temperature control throughout the pre-treatment process, further improving the quality of the galvanized product. The system also has a user-friendly design and is easy to operate and maintain.
Whether you have a small galvanizing facility or a large industrial plant, our pretreatment drums and heating systems are tailor-made to meet your specific requirements. We offer customizable options to accommodate a variety of production volumes and sizes. With our products, you can take your galvanizing operations to new heights of efficiency, productivity and quality.
Join the hot dip galvanizing pre-treatment revolution. Invest in our pre-treatment drums and heating systems and experience the transformative power of advanced technology. Trust our expertise and let us help you achieve the highest standards for your galvanized products. Contact us today to learn more about our innovative solutions.
Pretreatment heating
Use the waste heat of flue gas to heat all pre-treatment tanks, including degreasing, pickling and auxiliary plating. The waste heat system includes:
1) Installation of combined heat exchanger in flue;
2) One set of PFA heat exchanger is installed at both ends of each pool;
3) Soft water system;
4) Control system.
Pretreatment heating consists of three parts:
① Flue gas heat exchanger
According to the total amount of heat to be heated, the combined flue heat exchanger is designed and manufactured, so that the heat can meet the heating requirements. If only the waste heat of the flue can not meet the heating heat demand of the pre-treatment, a set of hot air furnace can be added to ensure the flue gas volume.
The heat exchanger is made of heat-resistant stainless steel or 20 # seamless steel pipe with a new infrared nano high-temperature energy-saving anti-corrosion coating. The heat absorption energy is 140% of the heat absorbed by ordinary waste heat heat exchanger.
② PFA heat exchanger
③ Drying oven
When the product with wet surface intrudes into the zinc bath, it will cause the zinc liquid to explode and splash. Therefore, after the plating aid, the drying process should also be adopted for the parts.
Generally, the drying temperature should not exceed 100 ° C and should not be lower than 80 ° C. Otherwise, the parts can only be placed in the drying pit for a long time, which will easily cause moisture absorption of zinc chloride in the salt film of the plating aid on the surface of the parts.